Equipment for production lines dedicated to sensitive products
Sauce, dairy product, yogurt, cheese, compote, drink, ESL milk, pasteurized milk
with DLC <90 days, acidic aseptic products
Decontamination levels:
3 to 5 log reduction on reference germs
Film
The Claranor sterilization unit is integrated online,
upstream of the forming step and before filling on one or two machine steps
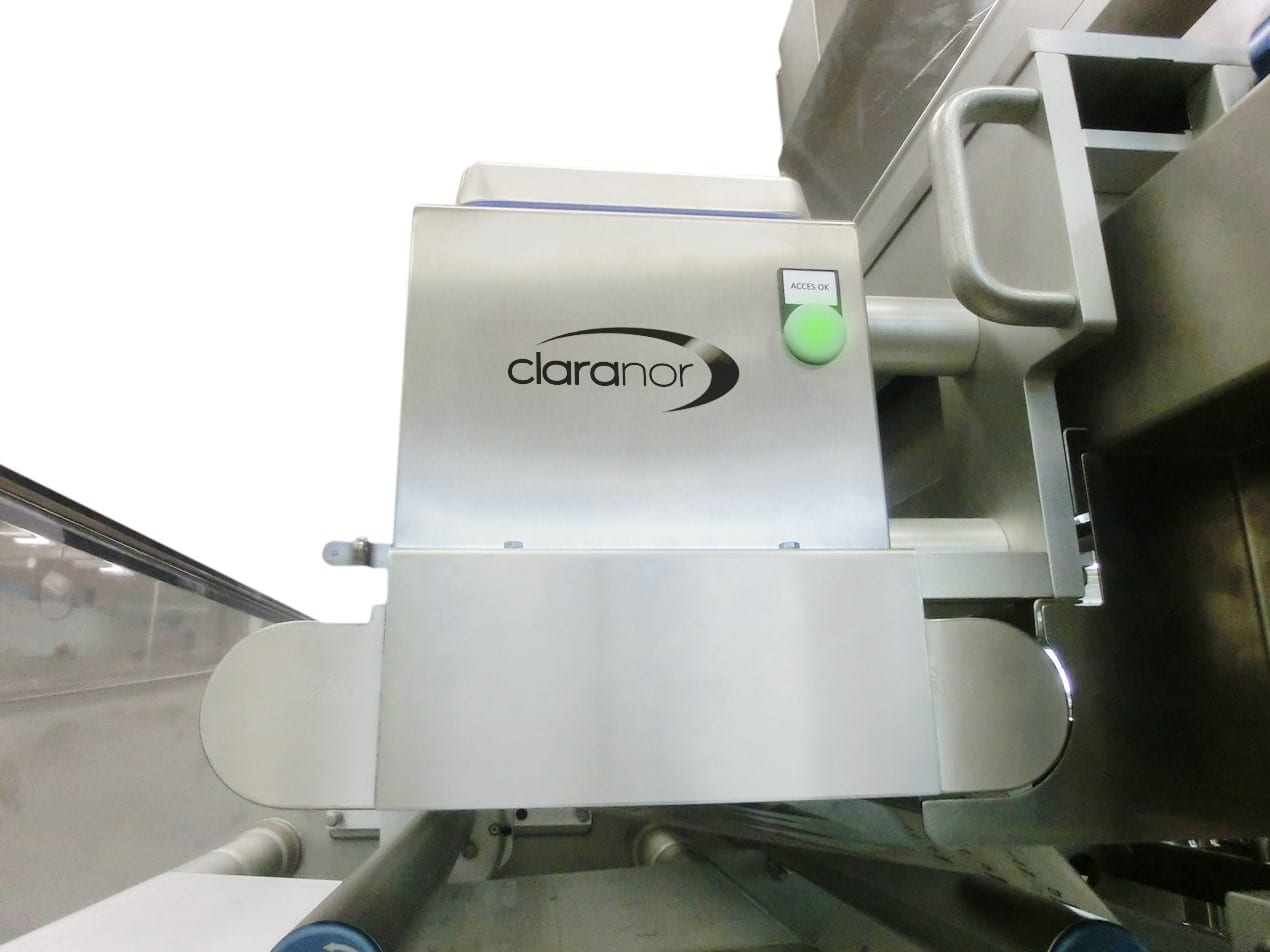
Up to 20 m/min
Decontamination of one or both sides of the film.
All types of materials (PE, PP, LDPE, Pla, composite…)
Max format:
Configuration adaptable to the bagger, vertical or horizontal
The integration of the equipment and the line shielding (optical protection) can be carried out by Claranor on a new or existing line.
- Synchronization with the production line.
- Instant processing.
- Non-thermal, it respects the packaging.
- Without risk of chemical residues.
- Economic and sustainable thanks to its very low energy consumption.
- Very competitive costs and simplicity compared to gamma-irradiation treatment.
FFS pouch
After the film decontamination, the forming and the filling of the pouch, decontamination of the neck / cap module before sealing on the pouch.
The Claranor sterilization unit can be integrated in line, on the circulation chute of the neck / cap module
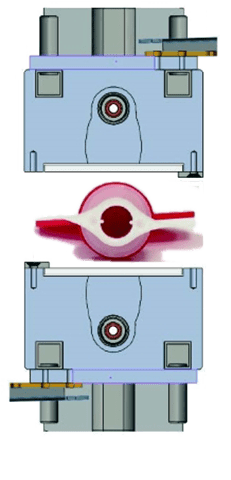
Pouch spout / cap
Up to
16 000 spouts/hour
Decontamination of the inside and outside surface of the neck
- Instant processing. Without risk of chemical residues.
- Economic and sustainable thanks to its very low energy consumption.
- Very competitive costs and simplicity compared to gamma irradiation treatment.
FS pouch
The Claranor sterilization unit can be integrated online,
above the filling neck and on the cap circulation chute.
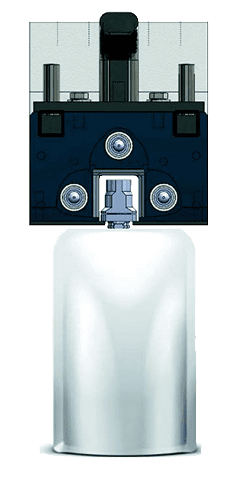
Spout pouch
Up to
16 000 spouts/hour
Decontamination of the inside and outside of the neck, after filling and before capping.
- Instant processing.
- Without risk of chemical residues.
- Economic and sustainable thanks to its very low energy consumption.
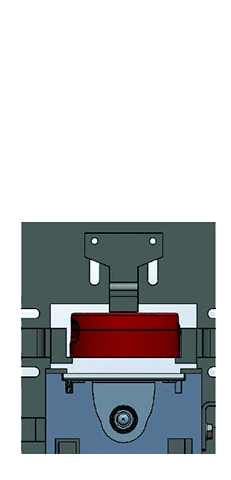
Cap
Up to
16 000 caps/hour
Decontamination of the inside of the cap,
part in contact with the product
All types of cups:
- shape
- and material